第3章 锂电池组的基本构造_低速动力锂电池维修与组装入门
锂电池组主要由电芯、保护板(BMS)、汇流排(镍带)、硅胶导线、绝缘青稞纸、抗震EV泡棉、捆扎纤维胶带、环氧板、防水胶、电芯支架、电池外壳等构成。
3.1 电芯
目前使用最多的电芯还是三元锂和磷酸铁锂为主,形状主要以18650为主,不过大单体电芯的PACK成本更低,对组装的工艺要求也更低,在低速动力电池领域越来越受到青睐。
设计一组电池如何选择电芯主要考虑的因素有:电压、容量、体积、成本等。以一组60V20Ah的电池组为例,如果用2000mAh的18650三元锂电芯做的话,60V的总电压就需要60V÷3.7V=16.2串,即需要17串串联,20Ah的总容量就需要20Ah÷2Ah=10支,即每一串需要10支电芯并联。电池组就是10P17S,总共需要电芯10P×17S=170支。可总结公式为:
电池组总电压V÷单支电芯标称电压V=电池组的串联数量S
电池组总容量Ah÷单支电芯标称容量Ah=电池组每串的并联数量P
电池组的串联数量S×电池组的并联数量P=电池组电芯的总数量
好的电芯才能做出好的电池,因此在组装前必须要经过一致性筛选,如果没有自动分选机也必须用内阻仪手动筛选,有些初学者因为供货商已经做过分容配对就省略此步给电池组埋下很大隐患。一致性筛选的原则是同一厂家同一批次的电芯配组,电压差不超过5mV,内阻差不超过3mΩ,如果采购电芯数量较少,达不到这个误差要求也要尽要能选压并和内阻差小配组。因此在采购电芯时一致性和容量是最核心的指标,目前小批量采购的电芯绝大多数都是B品电芯或拆机电芯一致性更显得尤为重要。
3.2 BMS电池管理系统(保护板)
保护板最基本的工作原理是通过时实监测电池组中每一串电芯的电压,判断充放电电压是否在锂电池安全合理的范围内,以决定充放电过程是否继续进行。通过监测充放电电流判断电流大小是否是在保护板额定电流的范围内,以决定充放电过程是否继续进行,以达到保护电芯,自动均衡,防止过充、过放、过流、短路等。
当前,保护板的功能越来越多也更加智能化,但是本着成本的考量应该根据锂电池组的用途合理选择保护板的类型。保护板保护电流的大小要根据负载电机的功率来计算,公式是:
保护电流A=电机功率W÷电机电压V×2
例如一辆60V的电动自行车电机是800W,800W÷60V×2=26.67A,就可以选用30A或者35A的保护板,保护电流越大价格越贵。类似这种低电压小容量的两轮电动车用锂电池就可以选择异口保护板,因为异口的主要区别是充电电流比同口小,小容量的电池组也不需要大电流充电,就可以选择更便宜的异口板。而电压在60V及以上,负载在2000W以上的高电压大容量电池组选择继电器式的BMS电池管理系统就更安全可靠。
3.3 汇流排(镍带)
电芯在串并联的连接中主要有镍带点焊、铜排或铝排激光焊、铜排或铝排螺栓紧固、金属导线锡焊连接等方式。
镍带点焊连接因为效率高,操作简单而被广泛应用,特别是18650、32650、21700等小型圆住体电芯的组装基本都以镍片连接为主。而镍带的材质又以铁镀镍带的经济性应用最广,常用的厚度有0.1mm-0.3mm,宽度有8mm-25mm以及各种支架专用镍片,主要根据电流的大小选择合适的厚度和宽度,横截面积越大承载电流的能力越强。
3.4 电芯支架
支架(图3-4)能很好的固定电芯,避免电芯间的直接接触,减少短路的风险,增加电池组的稳定性。使用支架会增加电池组的体积,因此可根据使用场景的要求选择是否使用支架。
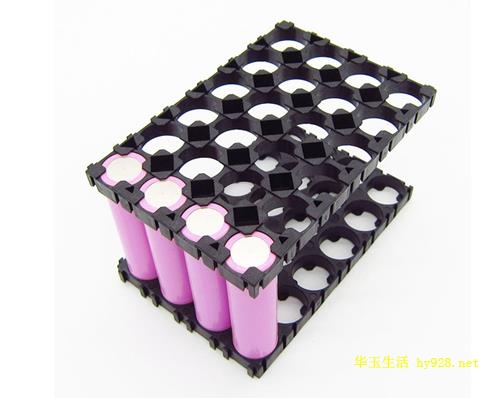
图3-4
3.5 绝缘和防震材料
常用的绝缘材料有背胶青稞纸、环氧树脂板、硅胶板、黄腊管、玻璃纤维穿线管等。常用的防震材料主要是EVA泡棉、珍珠棉等。
3.6 外壳
外壳种类很多,主要有塑料材质的和金属材质的,一般小型电动自行车用小容量48V8Ah、48V12Ah可直接用PVC热缩膜封装和塑料外壳封装,大容量的一般用冷轧板烤漆外壳、不锈钢外壳等金属外壳。
塑料外壳相对金属外壳有价格优势重量轻壳体绝缘,但强度不高散热效果一般。金属外壳重量更大,强度更高散热效果更好但必须做好壳体绝缘工作。各种材质的外壳都可以在网上淘到,也可以在当地找机加工的或不锈钢加工的定制。直接使用用PVC热缩膜封装的话必须保证电池仓是密闭干燥的环境且需要有一定强度的防护工能。
3.7 其它辅材
主要的辅材有固定用的:热溶胶、双面胶、玻璃纤维胶带等。防水用的单组分有机硅胶。连接用的焊锡丝、高温硅胶线、品字型插头、安德森插头、T型插头等。显示电池组信息的电流电压表等。
本书下载
|